Globally approximately 250 million barrels of water are
produced from oil and gas production.
Produced Water - A Montney Region Case Study
BACKGROUND & CHALLENGES
Produced Water is the byproduct of water produced during the oil and gas extraction process. It can be used several times, depending on the contaminants in the water. Produced water contains a variety of environmentally hazardous pollutants including heavy metals, bacteria, oils and grease, and various chemical additives. This type of water is generally highly saline and not suited for domestic purposes. In traditional oil and gas wells, produced water is brought to the surface along with oil or gas.
PROJECT DETAILS
Problem:
- Underperforming oil removal filter system
- High TSS, oil content, iron & bacteria, leading to high OPEX costs for chemical treatment
- ESG pressures and freshwater scarcity and sustainability
Project Specifics:
- Average treatment volume: 150 to 750 bbl/d
- Project duration – 4 months
- System configuration, Pre-Treatment + Swirltex UF System
PROJECT GOALS
For this client, the ideal solution required:
- Effective filtration of oilfield produced water, primarily for solids and oil removal;
- Consistent membrane permeate flux production of 100 LMH minimally; and
- Effective removal of key contaminants TSS < 50mg/L, Oil < 5mg/L, Iron < 10mg/L and Bacteria < 15mg/L.
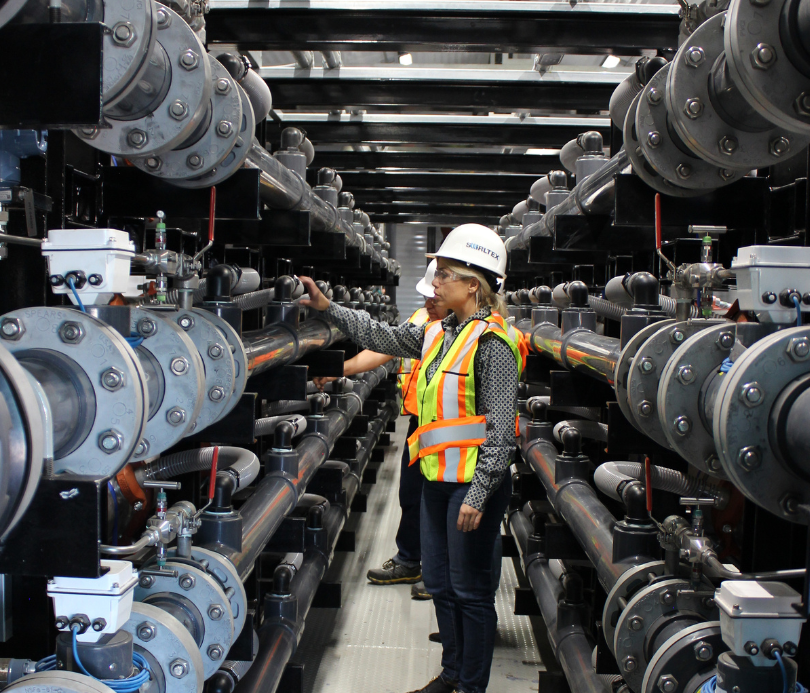
SWIRLTEX PROCESS
A chemical treatment step before membrane ultrafiltration is conducted to assist in the removal of solids and other contaminants to prevent membrane fouling and increase permeate production rate. Standard jar testing was performed until a chemical treatment package was optimized for the application; a 4-gallon sample was then prepared with newly optimized chemical dosages, mixed, and decanted.
The decanted/treated sample is then fed through Swirltex’s proprietary ultrafiltration technology for further purification of the sample. Swirltex then operates under their standard process parameters that have been carefully fine-tuned to minimize energy consumption while increasing permeate flux. Flux is collected in 10-minute intervals for 1 to 3 hours, depending on client requirements. Permeate is collected and sent for analysis at a third-party laboratory to ensure quality specs are met.
BENCH VALUE & FULL-SCALE SYSTEM
- Elimination of 20,000km per day with the reduction of 140 trucks per day and of travel associated. Water that can now be re-used rather than disposed of, equating to a GHG reduction of approximately 8,000 tones of CO2e/yr
- Significant downhole disposal saving and reduced impact on seismic activity concerns
- Chemical cost reduction and OPEX savings of $60-$100K per well pad
- Savings on pond cleanup, dredging, and de-sludging cost ($1M annually)
- Well production increases with clean saline water vs fresh water
- Up to a 75% reduction in freshwater consumption, thus saving an average of 357,000 m3 of freshwater per year
- Industry-leading, sustainable energy resource producer, ESG impact with sustainability goals.
- Full-scale Swirltex system installation Q2/Q3 2022, 20,000 bbl/d (3,000 m3/day)
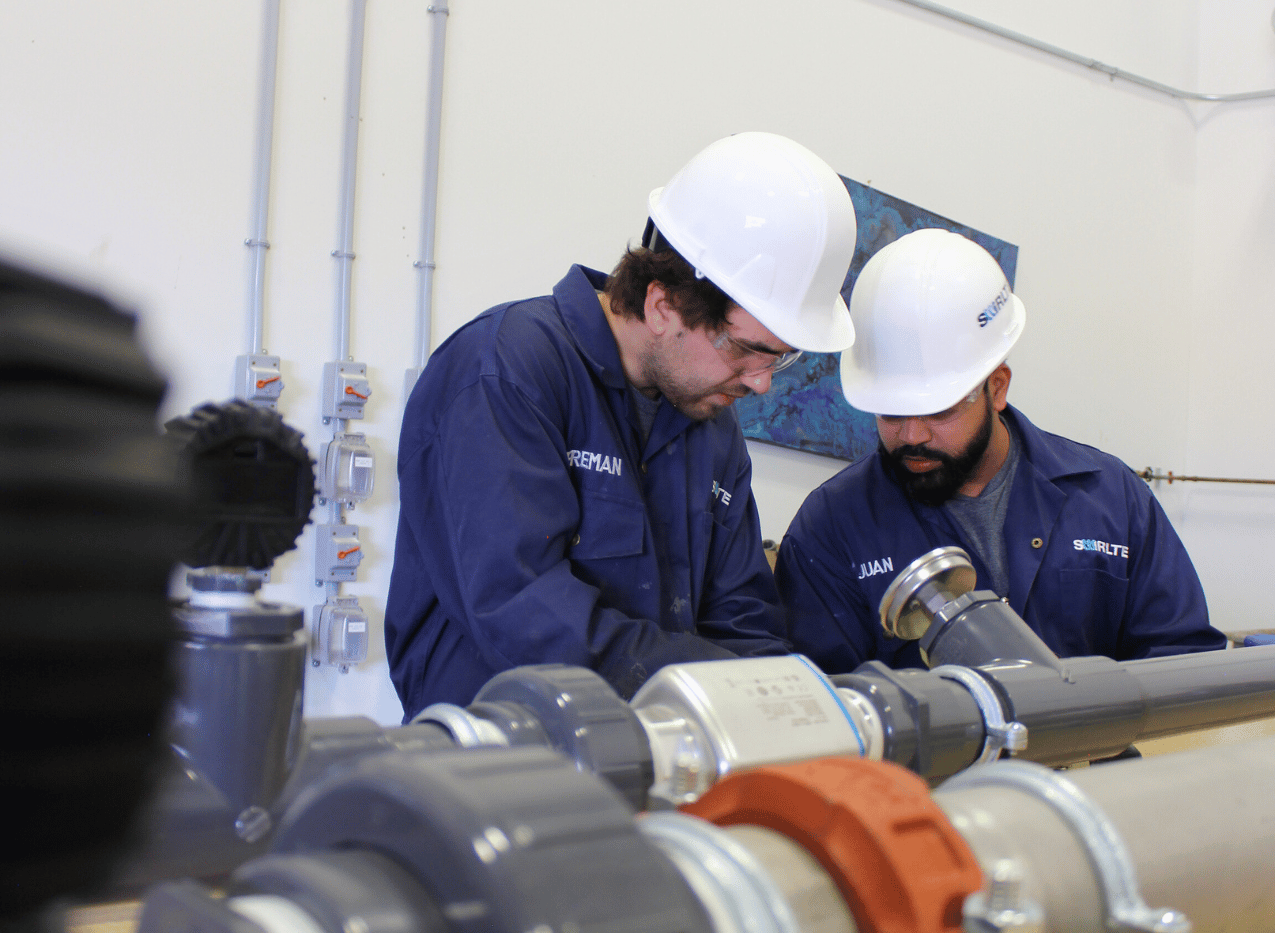
OUR RESULTS
Oil producers face challenges in removing TSS, iron, and oil, however, the Swirltex system shows exemplary results with minimal of 97% efficiency rate. The Swirltex technology helps oil and gas companies reclaim wastewater and accomplish their sustainability objectives. With low energy consumption and operational costs, the Swirltex system exceeds expectations in the wastewater solutions industry.
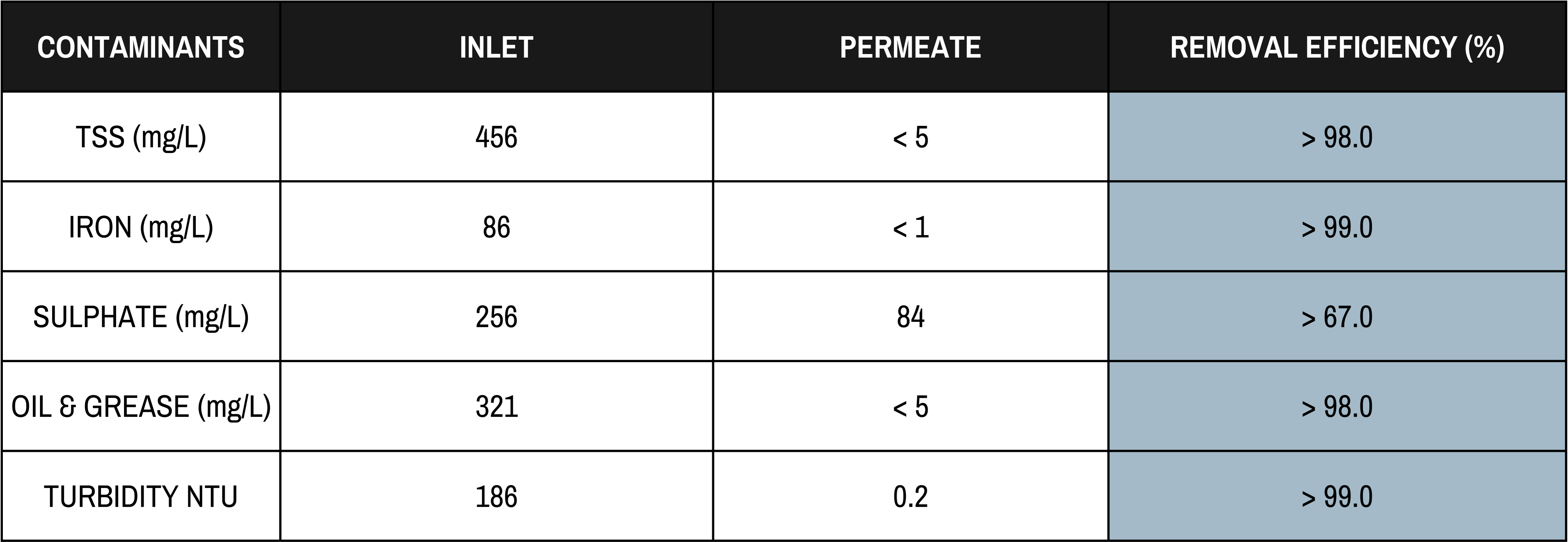
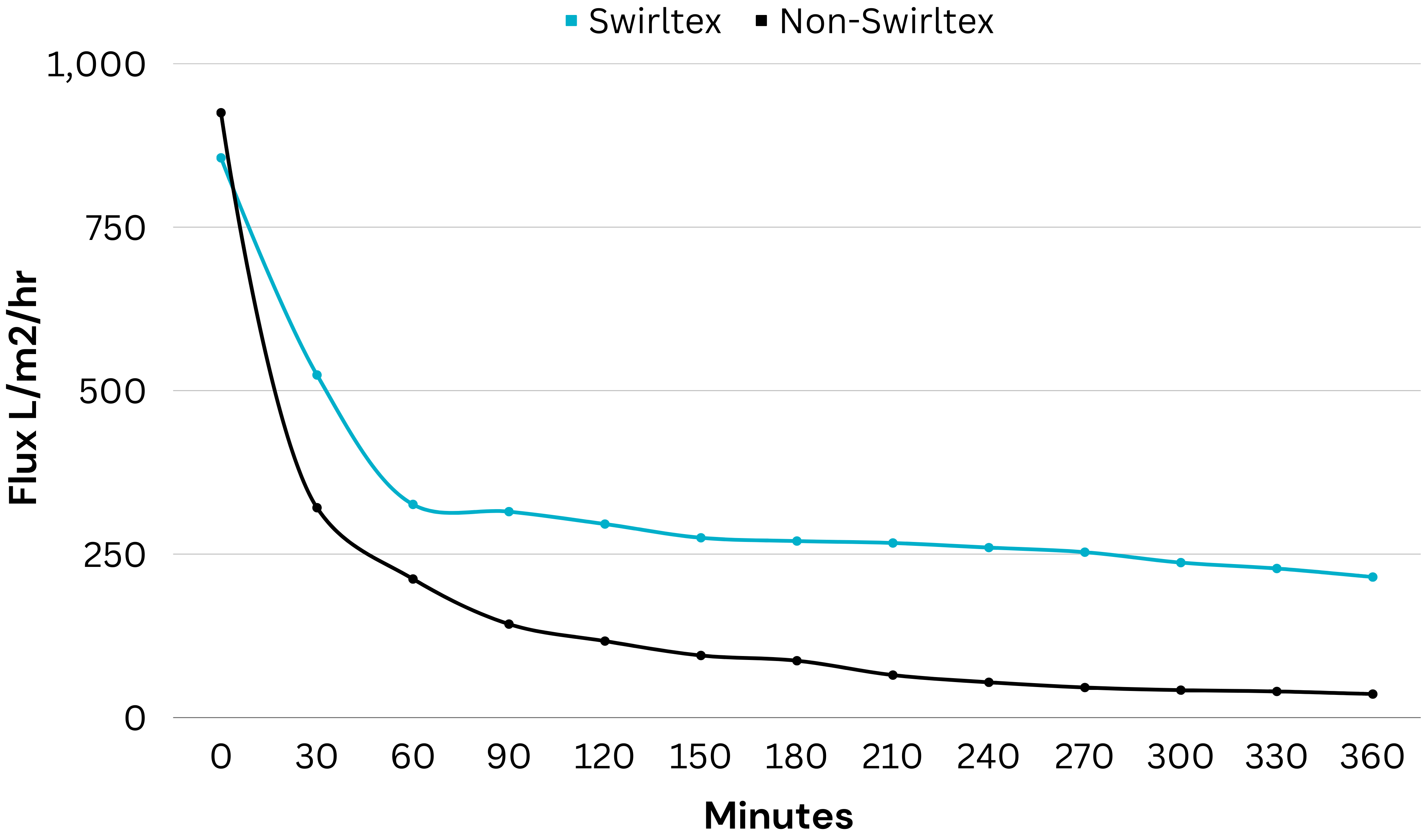
We were able to remove solids, iron, and oil with 220 Lmh flux production. Our innovative technology successfully treats wastewater as per the client’s needs.
Do you want to see exemplary results with wastewater filtration? Contact us for more information.